Last Update: March 10, 2018
The instructions in Part I. of this section are intended for the guidance of the individual user of the Electric Vehicle. It is assumed that the individual user is concerned with the primary principles of operation, in order that satisfactory use may be secured with the expenditure of the least time and labor in accomplishing these results in the Private Garage. When it is said that the electric vehicle requires little care and attention, the statement is made seriously but should not be interpreted to mean that it requires no attention whatever. This foreword may seem superfluous to some, but experience has shown that it has been this failure to observe the few simple but important rules that has been responsible for the majority of complaints against the electric car. The storage battery is neither mysterious nor complicated, but being constructed to work, must be kept in condition to do work. The attention required is very moderate indeed, but it is absolutely necessary.
Part II. of this section deals with the Care of Lead Storage Batteries in detail, from the time of their receipt from the manufacturer to the end of their useful life. This material has been collected and prepared to include garage practice so as to be of value to all concerned in the operation and maintenance of vehicle batteries.
PART I.
To charge a battery completely without excessive gassing, or heating, is the Book of Rules told in one sentence. The remarks which follow explain these three items.
Water. The height of electrolyte to be maintained at all times is one-half (34") inch above the tops of the plates. This is accomplished by the addition of pure water (preferably distilled) only. The addition of pure water should be made before charging and as often as required by evaporation.
Charging. Direct current only must be used for charging. Where alternating current only is available suitable apparatus (Chapter VI.) must be used to convert it to direct current. The polarity must be correct, that is, the positive terminal of the battery must be connected to the positive terminal of the charging supply circuit.
As it is necessary to ventilate the battery during charge, the battery compartment should be opened.
Under ordinary conditions it is not necessary to charge the battery more often than once a week unless over fifty (50%) per cent, of its capacity has been discharged. The battery should never be allowed to stand in a discharged condition.
The limitations imposed at any and all points of the charging operation are those of gassing of the cells and temperature of the electrolyte. Excessive gassing must not be permitted. Under all ordinary conditions begin the charge at the starting rate or higher of the two rates given on the name plate or in Tables I-V, and reduce the current in several steps, avoiding gassing and high temperature, until the finishing rate has been reached. Continue the charge at this rate until the voltage and specific gravity have risen to maximum values. At this point the cells will be gassing freely. It is better to stop the regular charge too soon than to overcharge. It is permissible to begin the charge at a higher rate, but care must be exercised to reduce the current should the cells gas or the temperature rise above the allowable limit.
Where any device or means is used in regulating the charge, especially as to the length of time, it should be adjusted so that a uniform gassing at the finishing rate, indicating the end of a regular charge, will be produced. This amount varies somewhat but is between five and fifteen per cent, more than the number of ampere-hours taken from the battery on the preceding discharge. This statement applies to ampere-hour meters, time clocks and rectifiers fitted with an automatic attachment.
Quick Charging or “Boosting.” At times where conditions may require the greatest possible amount of charge in the time available, the charge may be begun at a high rate, which must be reduced according as the gassing and temperature increase. The temperature must never be allowed to exceed 110° F.
Equalizing Charge. Bi-weekly at the end of the regular charge continue the charging at a rate not greater than the finishing rate until the specific gravity has stopped rising. When hourly gravity readings on the pilot cell are alike for four successive readings, then the overcharge may be discontinued.
Discharge. The battery should not be discharged below 1.7 volts per cell at its normal service rate and should not be allowed to stand in a discharged condition. If the full charge cannot be immediately given it should be put on for a partial charge. Beyond these limits the battery may be discharged as the requirements of the service demand, however severe it may be.
Gassing. In charging the battery, the rate at which the cells give off gas, is the determining feature. Violent gassing should at no time be permitted and whenever the gassing exceeds a very moderate amount, the charging rate should be lowered even though the length of time required for a charge be greater. Disregard of this precaution is probably responsible for the shortening of the life of most batteries.
Temperature. The temperature of the electrolyte should be kept below 100° F and never be allowed to rise above 110° F during charge. If necessary, the rate should be decreased or charging temporarily discontinued until the cell has returned to a normal temperature.
Electrolyte. The electrolyte should be maintained at the proper level by the addition of pure water. Never add acid.
At least once a month at the completion of the overcharge, readings of specific gravity should be recorded on all cells. Should any cell have a reading higher than 1.300 or lower than 1.250 when fully charged, it is evidence of trouble, such as a leaky jar, partial short circuit, or sloppage. The trouble should be found and remedied immediately. See “Electrolyte," page 72.
The specific gravity of the electrolyte should at no time be in excess of 1.300. Should this condition be found, some of the electrolyte should be withdrawn and water added to reduce the gravity of the solution. On the other hand, should the reading of any cell be less than 1.250, it may point to insufficient charging. If all of the cells have gradually decreased in specific gravity to below 1.250 and the cause not be insufficient charging, or lost electrolyte replaced by water, then it is safe to say that sediment has accumulated in the bottom of the jars, the battery should then be placed in the hands of a competent battery man for inspection.
The “Pilot Cell" referred to above is a convenient cell of the number which may be taken as representing the state of charge of the battery. There is a known variation in specific gravity during charge for each type of cell so that the amount of this variation be, low the specific gravity, when fully charged, will indicate the partial condition of charge at any time during charging process. The point at which the specific gravity reading of the pilot cell fails to increase and the cells gas freely may be considered the end of a regular charge.
Battery Out of Service. If the battery is to stand idle for any length of time, an overcharge should be given immediately before and immediately after the period of standing. Should this extend over several months, then a freshening charge should be given monthly at the finishing rate. If the idle period is to exceed four months or the treatment prescribed cannot be given, then the battery should be sent to a garage for the proper care.
Caution. Keep naked flames away from the battery, both while charging and immediately after charging as the gases liberated are explosive. Ventilation is required to dispose of them.
For handling the water or acid, only clean glass or earthenware should be used.
The battery should be kept in a clean condition and no foreign material allowed to find its way into the cells.
POINTS TO BE REMEMBERED IN THE CARE OF LEAD BATTERIES.
Unnecessary Charging. Is wasteful of current and uses up the life of the battery.
Standing Discharged. Is to be avoided in all cases as the succeeding charge would otherwise have to be for a longer time than usual in order to bring the battery into normal condition.
Adding Water. Pure water (preferably distilled) only should be used and added before charging. Under no condition put in acid unless distinctly specified.
Kind of Current. Use direct current only, connecting the positive (+) terminal of the battery to the positive pole of supply source.
TABLE VI. CHARGING VOLTAGES FOR LEAD BATTERIES.
No. of Cells. | VOLTS AT Start | VOLTS AT Finish. |
---|---|---|
12 | 26 | 31 |
14 | 30 | 36 |
16 | 34 | 41 |
18 | 39 | 46 |
20 | 43 | 51 |
22 | 47 | 56 |
24 | 52 | 61 |
26 | 56 | 66 |
28 | 60 | 71 |
30 | 64 | 76 |
32 | 69 | 81 |
34 | 73 | 87 |
36 | 77 | 92 |
38 | 82 | 97 |
40 | 86 | 102 |
42 | 90 | 107 |
44 | 95 | 112 |
46 | 100 | 117 |
48 | 105 | 123 |
50 | 110 | 128 |
- These voltages are approximate and are intended for guidance only.
- A battery when cold or new will show a higher voltage than an old one or at high temperature.
- It is not safe to regard a fixed voltage has the end of the charge, but a maximum voltage for the battery in question.
Ventilation. Open the battery compartment during charge and secure as much draft of air in the neighborhood of the battery as possible.
Gassing. Charge only until moderate amount of gassing is produced and not longer as it is wasteful both of current and battery.
Temperature. During charge do not allow the temperature to exceed 110° F. Either reduce the current or discontinue the charge temporarily, if necessary.
Caution. Keep naked flames away from the battery in order that the gasses may not be ignited.
PART II.
Unpacking. The crates or boxes containing the trays should be handled carefully and kept right side up to avoid spilling the electrolyte. They should be opened from the top and if necessary, one of the sides taken off for the removal of heavy trays. Care should be exercised in the handling of tools so that the jars may not be cracked. The trays and cells should then be cleaned off thoroughly and each cell examined for any possible damage. All the connections should be tight and clean as a loose connection would be liable to cause reduction in speed and mileage and eventually burn off. Should a loose connection be found, it should be lead burned or if that cannot be done at the time, then a temporary repair can be made by soldering but should be lead burned as soon as possible.
Should any broken or cracked jars be found, they should he replaced immediately. If there are no extra jars available, then the element should be removed from the broken jar and placed in a glass or earthenware vessel in acid of approximately 1.275 sp. gr. The plates must not be allowed to dry in air as it would require a very long charge to bring them back to a healthy condition. If the electrolyte level is lower than ^ inch above the tops of the plates, due to spilling and not to broken jars, then solution should be added to the correct level.
Batteries when shipped in the wet condition are shipped fully charged and require a freshening charge at the finishing rate of the make of battery in question, until all cells gas freely, before being placed in service.
When cells are shipped in the dry condition, they may either be assembled ready for the addition of electrolyte and the developing charge or as plates to be burned to the straps and assembled in the cells. As both of these shipments would require the developing charge they cannot be placed in service as can the batteries received in the wet state.
ASSEMBLING AND PUTTING NEW BATTERIES INTO CONDITION.
The parts must be unpacked, cleaned and examined carefully to see that they are in good condition and free from foreign material.
The plates must be grouped, that is, lead burned to the straps. This must be done by an experienced lead burner and when finished must be inspected to see that no lead has run down between the plates.
The plate lugs should be scraped clean and bright by a scraper of the kind used by a plumber and the plates for one ‘group placed in a burning rack or burning box as shown in (Fig. 12). Across the top of this box is fitted a piece of iron in which notches are cut correctly spacing the plate lugs. (Fig. 13.) The strap is then placed over the lugs and burned to them. The details of this assembly, as to the distances between plates and from the top of the plate to the strap, will depend upon the particular type and make of battery in hand. After the plates have been assembled into groups, the latter should be combined ready for the insertion of the separators. This is done by placing a perforated hard rubber sheet separator against the grooved side of a wooden separator. These pairs are then inserted between the surfaces of each positive and negative plate so that the flat side of the wooden separator is against the negative plate and the hard rubber sheet against the positive plate in each case. Should a separator, either wood or rubber, be broken while being placed in position, it should be discarded for a new one. No separators are placed between the surface of the negative plate and the containing jar. It is well to be careful that the edges of the separators are flush with the bottom of the plates so that contact between the plates may be avoided. The plates may be gently pressed together and are then ready to be placed in the jar.
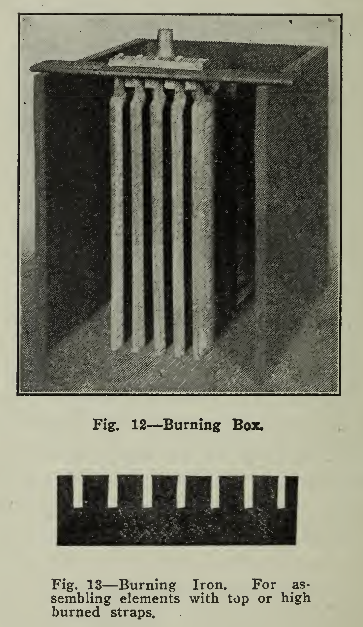
Fig. 13 — Burning Iron. For assembling elements with top or high burned straps.
With the element lying horizontally on the bench, the top of the jar, bridges crosswise with the plates, is placed around the element, being started carefully so that no edge of the plates or separators may catch on the rim of the jar. Only jars in good condition and thoroughly washed should be used.
It is necessary to secure the separators firmly in position so that they may not have an opportunity to float up from between the plates, allowing the latter to touch. For this purpose "hold downs" are used. When the groups are assembled with pillar straps, then a fin projects down sufficiently to keep the separators in place. With "L” straps, however, blocks of rubber or glass are used to keep the separators in a rigid position.
The cells are then ready for the acid, assembly in the trays and connections, so that the developing charge may be started. In several factories, the practice is to place the cells on a bench, instead of in the regular trays, in order that they may be kept cool by circulation of air during the initial charge. Where there is any tendency for the containing jars to warp or bulge from the heat, it is preferable to assemble the cells in the trays before beginning the developing charge as, otherwise, they could not be readily assembled in the trays. When the developing charge has been completed, the acid may be poured out and acid the proper strength immediately added to the correct level.
In some cases, where considerable developing is done, arrangements are made so that the jars may be placed in a tank through which cooling water may be circulated around the jars. An electric fan also helps considerably in keeping down the temperature of the cells during charging by circulating the air.
When preparations are completed, then the electrolyte of such specific gravity as recommended by the maker should be added to the cells to a level of Yz inch above the plates. The acid should not be above atmospheric temperature as the mere addition of acid to the cell will cause heating. It is necessary for the temperature of the cell to decrease to a normal value, such as that of the room, before the initial charge can be begun. As this may take from lo to 15 hours, it is generally advisable to add the electrolyte in the afternoon so that the cells may be allowed to cool over night and be ready for developing the following morning. Also, the acid will combine with the water in the separators so that the cells should stand for at least 12 hours before the initial charge is begun.
Having made the necessary connections, the charging should be begun at the rate given in the table and continued for the length of time necessary to charge the plates beyond any question of doubt. As the plates are received dry, and may have been standing in a dry condition for some length of time, they are in a somewhat sulphated state and need a long initial or developing charge to remove the sulphate. All of it must be removed by charging since if it is not removed at this time it will probably remain permanently.
Cells received from the manufacturer assembled and ready for developing are sometimes provided with hard rubber separators instead of with wooden separators because wooden separators unless maintained in a moist condition would warp and crack and be unsuited for service. To the cell thus assembled, it is necessary only to add acid of 1.170 specific gravity as described and continue with the initial charge.
The wooden separators are specially treated by the manufacturers to remove impurities, especially organic substances, which would greatly reduce the life of the plates. They are generally shipped in wet sawdust and should be kept moist by frequent sprinkling with water. If they are to be kept for any length of time they should be placed in a tank of pure water slightly acidulated with sulphuric acid.
The amount of charge necessary in developing a new battery will amount to about six times the rated ampere-hour discharge capacity, but must be governed solely by the indication of completeness of charge with very little gassing and not exceeding a temperature of 100° F. Should the temperature, during any part of the charge, rise above 110°, the charging should be temporarily discontinued until the normal temperature has been resumed. The charge should continue without interruption if possible until the voltage and specific gravity have reached a maximum. It is well to continue the charging for about ten hours beyond the point where these quantities no longer rise, in order that surety of completeness may be obtained. In order to obtain true density readings, since the specific gravity varies with the temperature, they must be corrected for the temperature changes on the basis of .001 specific gravity for each rise of 3° F., the standard being 1.280 at 80° F. Table No. 7, page 79, gives these corrections at a glance for the entire range ordinarily encountered in vehicle batteries.
After the charge has been completed, the electrolyte in each cell should be tested and the density adjusted to what corresponds to 1.280 at 80° F., maintaining the proper solution level of above the plates. The cells will usually increase in capacity for a number of cycles of charge and discharge during the early life of the battery, although the most rapid period of increase will be during the first 10 cycles. Should a high discharge capacity be required immediately when the battery is put into service, then several test runs of charge and discharge should be given before putting the battery into commission, in order to work up the capacity. In general it may be considered good practice to make a few test discharges after the developing charge, taking careful readings of the voltage and specific gravity of each cell in order to make sure that all cells have been developed evenly and sufficiently.
Assuming that the cells have been tested and found ready for service, they are then ready to be assembled in the trays. Before doing this, however, inspection should be made to see that they have been correctly assembled with separators in proper position and with no lead "flow downs" lodged on top or between the plates. When placed in position in the trays, the connections between cells should be carefully lead burned to the full depth of the straps and covers placed in position. If the cells are to be sealed, this should be done before the cells are placed in the trays and burned together. The jar and cover must be clean and dry for the compound to adhere. If acid or water remains on the hard rubber it will not stick. The sealing compound may be softened by being placed in a vessel heated over a moderate flame or the flame may be applied directly over the compound. When almost liquid it may be readily applied by a hot putty knife. For pressing into final position and finishing the sealing the putty knife should itself be heated in the flame. The sealing compound must neither melt at the working temperatures of the battery nor crack at low temperatures, so that the compounds supplied by the manufacturers should be used rather than untried material.
Cleanliness. It is necessary to maintain the cells, trays, terminals, connections and the battery space in the vehicle dry and free of electrolyte as a great many of the difficulties encountered in ordinary use can be traced to neglect. Should the electrolyte be slopped over the outsides of the jars and connectors or metal fittings, corrosion will result which will ultimately create loss of capacity.
CHARGING.
Service Charging. In charging, direct current only can be used in order to effect the chemical changes. Should alternating current only be available, then a suitable rectifying device must be used to convert the alternating current to direct current. These devices are described under "Charging Apparatus" Chapter VI.
Before charging is begun pure water (preferably distilled) should be added to compensate for evaporation, bringing the level of the electrolyte to one half inch above the tops of the plates.
As the normal condition of the plates in the discharged condition, is the lead sulphate state, the change to lead peroxide and spongy lead in the positive and negative plates, respectively, should be accomplished without wasting current or wearing the plates too rapidly. If the battery is steadily undercharged then the plates will gradually accumulate sulphate which will be evidenced by low specific gravity and low capacity. The longer the sulphate remains in the plate the more difficult it is to remove, that is, the more charging will be necessary. The desire therefore in bringing the battery to a fully charged condition is to send all of the sulphate from the plates back into the acid. In so doing, the current must not be so great as to cause excessive gassing since that would tear small particles of active material from the plate and thus shorten its life. Moderate gassing is permissible and at the proper rate, as explained later, is an evidence of the charged condition. The temperature must be kept within moderate limits also so that the chemical action may not be too rapid.
It is recommended that the charging be regulated so that temperatures in excess of 110° F. will not be reached. If necessary reduce the current or discontinue charging until the battery has returned to safe limits.
With the above in mind, it can readily be understood that when a battery has been fully discharged it should not be allowed to remain in that condition since the sulphate would be hard to reduce, taking an abnormal amount of charging to restore to healthy condition.
From this it is evident that a battery may be charged at any rate, no matter how large or small, as long as the temperature does not rise above 110° F. and the gassing does not become excessive. Under ordinary circumstances the most satisfactory results may be obtained by observing the following rules.
Begin the charge at the starting rate, given in Tables I-V, and reduce the current in several steps, avoiding gassing and high temperature, until the finishing rate has been reached. Continue the charge at this rate until the voltage and specific gravity have risen to a maximum value. At this point the cells will be gassing freely. It is better to stop the regular charge too soon than to continue too long. It is necessary to add bell tween 5 and 15% more ampere hours in charging than have been taken out on the previous discharge.
The voltage of the battery will rise during the charge to a maximum value, which is not necessarily, and which probably will not be, a fixed value. It will change with the age of the plates, the strength of the electrolyte and the temperature. New plates will have a higher final voltage than old plates and both will give higher final voltage with low temperature. These changes render charging by voltage alone as a standard a very unreliable process, so that specific gravity and gassing, with voltage as a check, give the best results. Providing that the battery is given the required care, the action in all cells will be practically uniform and one cell, conveniently located, may be taken as indicative of the others. Readings of specific gravity taken on this pilot cell therefore afford a simple and easy means of keeping the charging within bounds. The gravity varies slightly with the temperature and Table 7, page 79, is given so that corrections may be easily made, to the density of 80° F.
While the battery should not be allowed to stand in a discharged condition, it should not be charged unless necessary. If less than 50% of the capacity has been discharged then a charge should not be given unless the subsequent discharge will require more than the capacity available. To run the car a comparatively small percentage of its mileage and then give approximately a full charge is evidently a waste of current and battery. The number of cycles of charge and discharge depends upon the conditions of service, so that wasteful charging dissipates not only current uselessly but plate life also.
A very convenient method of automatically recording and calculating the charging necessary is accomplished by an instrument known as an Ampere-Hour Meter, Fig. 14. This instrument is furnished with a dial, and hand revolving in a counter-clockwise manner on charge, and clockwise manner on discharge. (This order is reversed by some vehicle manufacturers.) During the discharge a glance at the meter gives a direct reading of the discharge capacity used, so that knowing the total discharge capacity available, the amount remaining is readily given. The total available ampere hour capacity divided by the number of miles under average conditions of driving will give the ampere hours per mile. This figure depends upon the condition of vehicle, roads and load carried. Taken under normal conditions, however, this figure divided into the capacity gives the average mileage obtainable on one charge of the battery. If the capacity be 120 ampere hours and the ampere hours per mile be 3, then approximately 40 miles is available per charge of the battery.
During charge the pointer revolves counterclockwise until it reaches the vertical position where it remains against a stop, showing full charge. An adjustment is provided allowing the charge to be made from 0 to 30% greater than the discharge.
This setting is arbitrary and depends upon the service conditions. Additional wiring is provided so that a circuit breaker may be closed when the pointer reaches the stop, disconnecting the battery from the charging circuit.
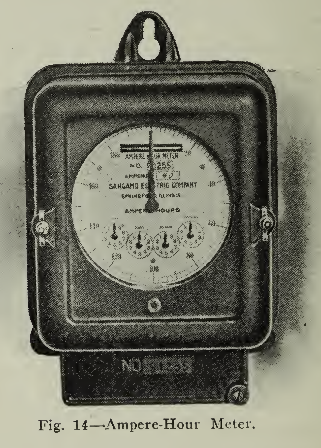
This feature is very convenient for effecting the desired charge with little waste and minimum attendance as well as for discontinuing a charge during the night.
EQUALIZING CHARGE.
Under the head of charging the instruction was given to discontinue the charge too soon rather than to charge too long. Under this heading the instruction is to overcharge too long rather than too little. The reason for this is that the overcharge is designed to bring each cell of the battery to a fully charged condition. This is accomplished by continuing a regular charge at the finishing rate three or four hours after the pilot cell has reached a maximum of specific gravity and voltage readings. Hourly readings should be taken. When several of these are alike the overcharge may be discontinued. Before beginning this charge inspection should be made of all cells and pure water added to bring the solution to the correct level of one-half inch above tops of plates.
The regular charge should be discontinued when the battery is approximately charged so that no harm may be done by constantly overcharging. Assuming that the plates are not fully charged each time, the capacity will decrease gradually as indicated by the lower specific gravity readings. It is necessary to send the acid held in the plates back into the solution, recovering the full capacity, by the periodic overcharge. Therefore, should the car be charged and discharged daily, a weekly overcharge would be most satisfactory, while on the other hand if the mileage required be small and the regular charges infrequent then a bi-weekly overcharge is sufficient to keep the plates in healthy condition.
When a battery is to remain idle for any length of time, a freshening overcharge should be given at least monthly and preferably bi-weekly while not in service. Should the period be for over four months or facilities for this charge not available then the battery should be taken apart and stored dry as explained under "Taking Out of Commission" page 91.
CHARGING OVERNIGHT.
There are a number of applications in which it is impossible for attention to be given the battery during charge, such as, charging overnight or when no attendance can be given. In this case the battery may be placed on charge at a rate never more than 2/3 of its regular “starting rate" and allowed to remain on charge, the current gradually decreasing until discontinued either by hand or by an automatic device. The number of ampere-hours required should be estimated by adding 10% to the capacity in ampere-hours taken from the battery on its previous discharge. Thus the number of ampere-hours required to fully charge the battery, divided by the number of hours available, will give the average current for the charge. When charging from a constant potential circuit, the current will decrease gradually throughout the charge. This is most rapid at the beginning due to the heating of the charging rheostat and the rise in counter electromotive force of the battery. For this reason the rate may be set two or three amperes higher than the average current at the beginning, but a rate exceeding Yz of the “starting rate" should not be used unless attention can be given.
The limiting conditions of charging in this manner are gassing and temperature and what has been said in the previous paragraphs is also true in this case. Excessive gassing or high temperatures must not be permitted so that it will be necessary to give frequent attention, observing the temperature and gassing during the first few periods of charge, in order that the results may be obtained without running the risk of ruining the battery. After these experimental charges, conditions will be known approximately and a close, estimate can be arrived at for subsequent unattended charges.
There are a number of automatic means for regulating charging. The ampere-hour meter has been described. When wired to a circuit breaker it discontinues the charge when the required number of ampere hours have been supplied. The hand on its dial rotates to its zero position making a contact which closes the trip circuit of the circuit breaker.
A time clock may also be secured that will open the circuit at a predetermined time. Mercury Arc Rectifiers are furnished with attachments which not only restore the arc in case the service has been discontinued, but which also cut-out when a certain maximum voltage has been reached. None of these devices control the rate of current during the charge so that while the time during which the charge lasts may be correct, the rate of charge depends wholly upon the attendant, and should be kept as low as possible in order that the limitations of temperature and gassing may not be exceeded. Whenever possible, attention should be given to obviate any damage from excessive heating or gassing.
BOOSTING OR EMERGENCY CHARGING.
Charging of this nature is particularly adapted to conditions under which the capacity required from a battery is greater than the normal output for which it is designed. If the vehicle requires a boost in order to reach its garage or cover its route, after a trip which has taken practically all of its available capacity, or if an extra trip is contemplated which it is estimated the remaining capacity will not meet, then this emergency charging is exceedingly useful. During certain times of the year the road conditions or extra heavy loads make an extra charge necessary. This may be given either when the battery has been fully discharged or during a noon hour, or other similar period of rest. The advantage of the noon hour period is that no unnecessary time need be . spent, but on the, other hand, the charge will be limited to approximately one hour. The use of boosting charges makes it possible to design the battery for average requirements instead of carrying sufficient battery capacity for maximum requirements.
In giving a charge at a high rate, the limiting features are temperature and gassing. The temperature must not be allowed to rise, under any circumstances, above 110° F. and should be kept as much below 100° F. as possible. In the summer it is evident that this will limit this method of charging. The gassing should at no time be permitted to be excessive and it is well to keep it a minimum, The more fully the battery is discharged the higher may be the starting rate of the boost so that a fully discharged battery may receive the same amount of charge in a shorter time than a battery which has been but partly discharged.
The standard instructions for giving a rapid charge are to start the charge at a rate 50% above the normal charging rate, gradually reducing the current step by step until the finishing rate is reached, when the charging may proceed as described under "normal" service charging. The limits of gassing and temperature must be very rigidly observed or damage will result. The indications of the extent of charge are voltage, specific gravity and gassing as have been explained.
A method for boosting which has been developed
and recommended by several prominent storage
battery engineers, making use of the ampere-hour meter is as follows: Make the boosting rate in
amperes equal to the quotient of the ampere-hours
discharged from the battery divided by one plus
the time available for boosting in hours. That is,
if the ampere-hour meter shows 200 ampere-hours
discharged and one hour available for charging
then the rate would be 200 / 1+1 = 100
amperes for one hour. If but 15 minutes should be available then the current could be as high as 200 / 1 + .25 = 160
amperes. It is said that the gassing point
will just be approached at the end of the specified
time, when the rates are determined by the above
rule.
Experience has also shown that when a battery is placed upon a constant potential circuit of 2.3 to 2.35 volts per cell without intervening resistance, that the charging rate in amperes will then very nearly equal the state of discharge in ampere-hours at any time.
Having in mind what has been said under this heading, it is evident that a charge may be begun at any current rate, several times the normal charging rate if necessary and reduced according as the gassing and temperature dictate. This method is very convenient and will admit of very flexible operation of the electric vehicle, but it is recommended for use only in the hands of competent attendants.
CHARGING OUT OF THE VEHICLE.
When it is necessary either for test, after repairs, or with reserve batteries to charge them out of the vehicle on a bench, then the operation familiarly known as a "Bench Charging" or “Discharging” is identical with that described for the battery in the vehicle in nearly all particulars. It admits of ready access to each of the cells during the entire charge and discharge and enables the operator to make complete and full readings of voltage, specific gravity, temperature and such other inspection, as may be required, upon each cell of the number.
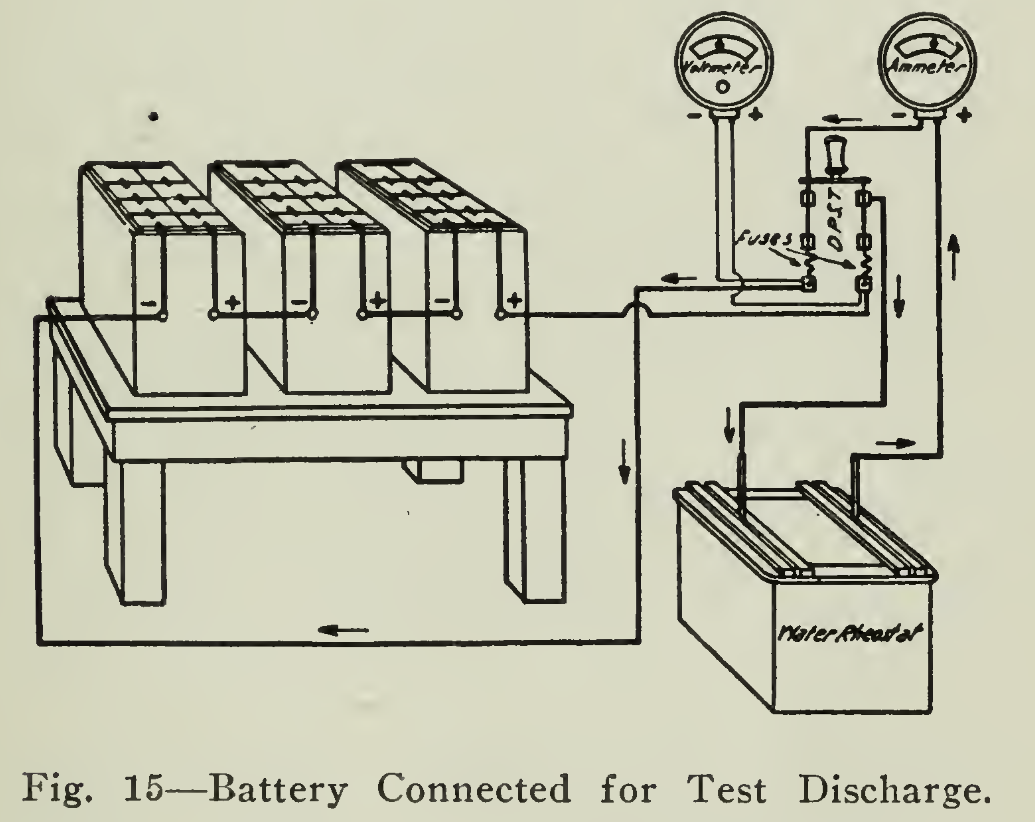
The connections from the battery to the charging source are not effected by means of the charging plug and receptacle, as the- battery is disconnected from the vehicle wiring. Should there be necessity for considerable bench charging then it might be convenient to have an extra receptacle the terminals of which would admit of rapid but secure fastening to the battery terminals.
When the battery is in the vehicle it is discharged by passing the current through the motor, which does useful work, such as propelling the vehicle. In this case, however, the current is to be dissipated in the form of heat by passing the current through a suitable resistance or rheostat. The positive and negative terminals are connected (Fig. 15) through the rheostat or suitable resistance and an ammeter. The ammeter indicates the current rate of discharging in the same manner as that of charge. The rheostat used in charging will not have sufficient resistance for discharging the battery especially at the beginning of the discharge. When the voltage is high, additional resistance must be placed in series.
One that is very convenient and easily constructed is what is known as a Water Resistance. This is constructed by making use of a wooden tub or half-barrel. Two wooden sticks or rods are laid parallel across the top of the barrel and from them are suspended two metal plates (iron grids or lead iron) parallel to each other One wire from the battery is connected to one of these plates through one pole of a double pole switch, the other plate is connected through the ammeter to the other pole of the switch and thence to the other battery terminal. Before starting to discharge, all the resistance should be put in the circuit in the charging rheostat ordinarily used and the plates in the tub separated as far as possible.
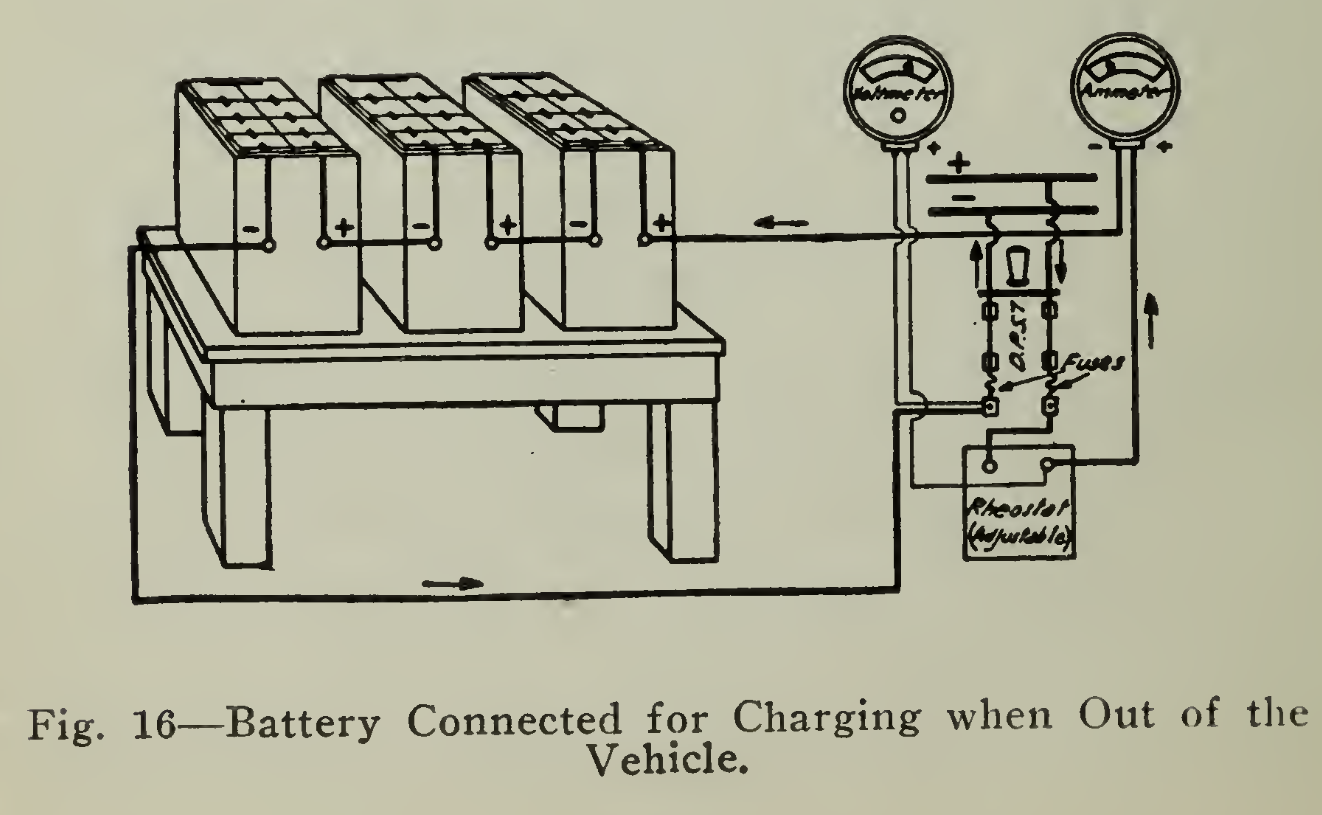
The tub can then be filled with clean water and the switch closed.
Small quantities of sulphuric acid added to the water from time to time will increase the current and will serve in the same way as moving the plates toward each other. It is preferable to have the plates remain fixed and to add acid, increasing the conductivity of the solution as short circuit between the plates will be less liable to result. This resistance in series with the regular resistance will give easy and fine regulation of the current. The diagram shows the method of connecting the parts and taking the readings.
In making the connections referred to, the wires or cables should be of such size as not to heat unduly at the maximum current of discharge. The size of wire used in the vehicle is sufficiently large.
INSPECTION.
An inspection should take place at least every month in order that slight troubles may be remedied before they become serious and serious ones remedied immediately. If the battery compartment is constructed so that the inspection may take place with the trays in the vehicle then it is not necessary to remove them. If this is not the case, however, then it would be necessary to disconnect the end leads to the controller and slide the trays out. A low truck on rollers is found to be very convenient for this work as the truck can be run up along side or in front of the battery compartment and the tray placed upon it. In fact, an adjustable platform truck is manufactured for this service. The rubber plugs should be removed so that the tops of the plates may be seen. The level of the electrolyte, which should be one-half inch above the plates, should be determined by means of a piece of one-quarter inch glass tubing or by inserting a clean strip of wool or hard rubber. If the level is not correct it should be made so by adding pure water. The connectors between the cells should be examined and if any are found to be weak, loose or broken they should be repaired. After cleaning, the trays are then ready to be placed in commission.
ELECTROLYTE
The electrolyte used in the lead type cell is a mixture of pure sulphuric acid and pure water. This mixture, known as dilute sulphuric acid, should be chemically pure, but no harm will result if certain chemicals are present which do not affect the activity of the cell. Impurities such as iron, copper, platinum, mercury, arsenic, chlorine, nitric acid and acetic acid must never be present.
Always pour acid into water, never water into acid.
When acid and water are combined, a chemical reaction takes place and considerable heat is developed, the amount of heat depends upon the relative proportion of acid and water. Should a small quantity of water be poured into a vessel of acid, the water would immediately be turned explosively into steam with the result that a part of the mixture of water and acid would fly up from the vessel and probably seriously injure the face and hands of the operator. Ordinarily it is more advisable for the user to purchase electrolyte ready for use or if wanted in quantity, acid of 1.400 specific gravity will usually be found of sufficient strength.
Owing to the heat generated it is necessary to allow the solution to cool before taking the specific gravity of the mixture inasmuch as the density changes with the temperature. By referring to Table 7, on page 79, the real density at any temperature may be found and compared with that at a standard temperature of 80° F. This change in specific gravity is due to temperature and is a physical change only. However, when electrolyte is used in the active cell then another change takes place which has already been described, that is, a variation in density due to chemical change, the acid being absorbed by the plates. The acid itself is broken up, the sulphate part combining with the plates and the hydrogen part combining with the oxygen set free to form water in the electrolyte.
Thus the specific gravity of the cell will decrease as the cell is discharged and increase upon charge, returning to the original value upon charging to the same extent as originally, making allowance for the temperature change. The density increases until all the acid is out of the plates. In some cases where the plates are badly sulphated, that is where the sulphate has hardened, excessive charging will be required to remove it. During such a charge the rise in gravity will be very slow.
This specific gravity or density is measured by simple instrument known as a hydrometer. This very useful accessory is constructed of glass weighted at the bottom with lead shot and possesses a calibrated scale so that when immersed in the liquid, the reading of the scale at the surface of the solution is the specific gravity of the electrolyte.
For convenience in making this reading the hydrometer is usually placed in a second glass tube of sufficient diameter to allow the hydrometer to float. This hydrometer syringe furnished with a pure rubber tube at the lower end and a rubber bulb at the upper end permits electrolyte to be drawn from the cell into the barrel and to float the hydrometer. In this manner the gravity readings of the electrolyte in all the cells of the battery may be readily and quickly determined. For ordinary charging it is necessary to read the gravity of a few cells only, "pilot cells" assuming that these are characteristic of the battery. At the inspection and reforming periods, however, each cell should be carefully gone over.
The amount of the electrolyte required in the cells depends upon the size of the containing jar and the number and size of plates and is usually given in the manufacturer’s catalogue. However, it is a simple matter to remember that whatever this size may be, the electrolyte in any cell should be one-half inch above the tops of the plates so that sufficient may be available for evaporation or sloppage without exposing any of the plate surfaces, which is injurious.
The specific gravity, when the cell is fully charged, will be approximately 1.260 to 1.280, depending upon the condition of the cell and temperature ; when the cell is considered discharged, the gravity will have fallen 100 points more or less depending upon the type of battery, owing to the, removal of sulphuric acid by the plates. From this it can be readily understood that the amount of charge can be at once found by taking hydrometer readings, knowing the upper and lower limits for the particular battery in question and correcting for temperature change,.
Throughout the instructions emphasis has been laid upon the fact that distilled water only should be used to replace evaporation. The reason for this is, that adding acid would change the gravity of the cell and so there would be no check upon its condition with the effect that the strength of the solution would gradually become too great for satisfactory results, sulphating the plates and reducing the efficiency of the cell. It is obvious that by changing the gravity through such means that no indication of the state of charge would be reliable. High density when thus given will shorten the life of the battery.
Should a leaky cell be found it would be necessary to place the element in a new jar and fill with electrolyte of 1.250 specific gravity. After charging at the "finishing" rate until the gravity of the leaky cell has ceased to rise, the density should be finally adjusted to the correct point (1.270-1.280).
After the overcharge has been given, gravity readings should be taken of all cells of the battery. If the battery has received the proper overcharge and it is evident that low specific gravity in any cell is due to sloppage or spilling and not undercharging, then some of the electrolyte should be withdrawn and acid added to bring the gravity up to that of the other cells. If the specific gravity be higher than 1.300 in any cell it should be reduced by withdrawing electrolyte and adding pure water. This “equalizing” should be done only when low density is not due to insufficient charging, because the gravity is the indicator, and tampering with the indicator will only give temporary, misleading results.
Should there be doubt of the purity of the water or electrolyte or indications of trouble from them, then samples of one quart of water or eight ounces of solution should be sent to the manufacturer for test.
Electrolyte — Low Cells. There are many causes for low cells, among which may be mentioned, insufficient charging, leaky jar, loss of electrolyte by spilling, broken parts or presence of foreign material. The remedies for these may be divided into three classes.
The first and simplest is to treat the cell electrically, by prolonged charging at a low rate, until the gravity and voltage reach a maximum. This charge should be too long rather than too short, for if not complete the trouble will be only temporarily removed.
In the case of leaky jars it is necessary only to replace the jar and give a long charge at a low rate, after which the gravity should be adjusted to the same value as that of the adjoining cells. When water has been added to replace spilled electrolyte then the gravity may be equalized by adding acid enough to bring up the density. If foreign material has found its way into the solution, then the solution should be renewed and the water used to replace evaporation tested for impurities as explained under "Electrolyte." Salt and iron are most likely to find their way into the cells. Salt will be indicated by the offensive odor of the chlorine gas given off during charging and iron by the dirty yellow color given to the positive plates. Similar evidences are given by other impurities.
If these are found present, the cell should be dismantled irrespective of its state of charge or discharge, as explained under "Sediment," washed and reassembled with pure electrolyte of the same gravity as that removed and new wood separators and given several charges and discharges. After these and while discharged, again take the cell apart, rinse the parts well and reassemble with new electrolyte of 1.200 specific gravity. Then give a long charge. All precautions should be taken as detailed under “Sediment,” p. 82.
Taking the cell apart to inspect for sediment, condition of separators, short circuits between plates, etc., includes only dismantling the cell and reassembling into the original condition as nearly as possible.
When it is necessary for inspection or in testing to determine the cell voltages throughout the charge and discharge periods, the readings are taken with a low reading voltmeter. An accurate instrument should be used for this purpose and should be returned to the manufacturer or competent laboratory for calibration at least twice a year.
Probably the most convenient form of voltmeter is one which has a double scale, one scale reading 0 to 150 volts for determining a complete battery or line voltage and the other scale reading 0 to 3 volts. Where there is sufficient use for a low reading voltmeter, an instrument with but one (low reading) scale might be of increased value for taking the individual cell and cadmium readings. Voltmeters are delicate and will not stand abuse with impunity. Care should be exercised not to apply the 0 — 3 volt terminals to the 110-volt circuit or over more than one cell, as the instrument would very probably be burned out. Also the needle should not be sent in the wrong direction as the violent shock would be liable to bend it out of shape.

Voltage readings of the cells are of value only when taken, while current is passing through the cells either in charging or discharging. They then serve to indicate the condition of the cell under all its states of health.
The leads or small rubber covered copper wires from the voltmeter terminals to the points across which the voltage is to be measured should be of sufficient length to reach from the terminals of the meter to the cell at the most remote corner of the battery, so that readings of every cell may be quickly obtained. A very convenient method of making good contact rapidly between the leads and the cell terminals is to fasten the leads to sharp metal points held in wooden handles. These may be easily constructed by inserting a wire nail into a wooden handle and soldering the lead to the nail. These are familiarly known as "stickers" or "stabbers." One should be conspicuously marked positive (+) or the wire from it knotted at both its ends in order that the positive lead may be placed upon the positive pole and not on the negative by accident.
During charge, voltage of a cell will rise from* 2.2 volts to 2.5 — 2.6 volts and during discharge will decrease from 2.1 to 1.7 volts. The discharge should not be carried below 1.7 volts per cell as the voltage drops very rapidly after that point and an abnormal amount of charging would be required to bring the cell back into condition when thus over-discharged. However, should the rate of discharge be higher than the normal or catalogue discharge rate, then the limiting voltage will decrease with increase of current and a somewhat lower voltage is permissible. This is the condition which obtains when cells are discharged under service conditions. When they are being tested, the catalogue rates of discharge should be maintained in order that a definite basis for comparison may be secured. The manufacturers catalogue discharge rate is a 4, 4 1/2, 5 or 6 hour discharge rate, depending upon the type and thickness of the plates.
By a study of the voltage readings of each cell of the battery during the progress of the charge, it is possible to determine accurately how the cells are reaching their state of completely charged condition and whether all increase uniformly.
In a similar manner half-hourly readings taken during the discharge show the relative capacities of the cells. Those which give noticeably lower voltages than the rest during the discharge are called ‘'low cells,” and if extra charging does not restore them to the condition of the other cells then it is necessary to treat them as explained under "Loss of Capacity" (page 88).
SEDIMENT
As explained in the description of storage batteries used in vehicle service, the “Pasted Type” plate is used in practically all cases. Throughout the life of the plates, the active material is slowly disintegrated and forced off the plate surface, gradually finding its way to the sediment space in the bottom of the jar. Practically, there are two limits lo the allowable amount of sediment. When the plate has lost sufficient active material to reduce its capacity abnormally then it is more economical to install new plates than to operate with the old. If the space at the bottom of the jar should not be sufficient lo accommodate the total amount of sediment forced off the plates before this condition, then it will be necessary to dismantle the cells and remove the sediment in order to prevent short-circuiting of the plates by the waste material. The proper adjustment of these two limitations is taken care of in design, by the proportioning of the cells, but as space is not sufficient in the electric vehicle to allow larger size jars than are absolutely necessary, it is found more practicable to remove the sediment from the cells at intervals. This is not true in all cases as there is a strong tendency at this time to assemble medium thin or thin plates in high bridge jars so that no cleaning is required during the life of the positive plates. The positive plates are those, which are deteriorated most rapidly inasmuch as the active material of the positive plate is very much less coherent than the active material of the negative plate. Hitherto it has been considered good practice to subject a set of positive plates to one cleaning during their life and using one set of negative plates with two sets of positives. As mentioned above, however, the introduction of thinner plates and special types of positive plates has developed the design of a negative plate of life of approximately that of the positive plates with which it is to operate.
By these means, under certain conditions of service where these types of plates are recommended, cleaning is avoided. The process is given in detail, as it is standard practice to remove the sediment from the cells except in the cases mentioned.
The length of time for which a battery would operate without necessitating cleaning, depends upon all the peculiarities of the service and cannot be predetermined accurately, in fact, that is not necessary. The better the treatment and handling that the battery receives, the less frequent will be the removal of sediment. Increasing quantities of sediment make themselves known by decreasing capacity, the more conspicuously by the gradual decrease in specific gravity taken when fully charged. This material resting at the bottom absorbs the sulphate of the acid, decreasing its density so that ordinarily when the density has fallen below 1.250, over the cells of a fully charged battery, it may safely be assumed that the cause is due to the collection of sediment, provided that water has not been added to compensate for solution spilled or slopped from the jars.
After 50 to 75 discharges, one cell of the number should be cut out, the depth of sediment recorded, and replaced. In doing this, the element should be removed without disturbing the separators and without shaking up the sediment while pouring out the acid. Should only a small quantity of sediment be found, then the cell should be washed out, the element replaced, solution returned and the cell burned into position. An estimate of the growth of sediment may be formed from this, as to the length of time necessary before cleaning, when the sediment has reached to a height of below the bottom of the plates. Checks may be made upon the rising of the sediment level by removing other cells at intervals for inspection.
When sufficient material has accumulated to reach to within below the plates, then the battery should be given an overcharge and the cells disconnected.
Where "L" or "T" straps are used, a hack-saw is most convenient for cutting the cells apart. If they are assembled with pillar straps then a drill, in a carpenter's brace, can be used to bore down to the depth of the strap allowing the connector to be easily removed. If they are handled carefully in this manner they may be readily burned, in reassembling without renewal. The use of a Connector Puller as illustrated and described on page 106 will be convenient in disconnecting cells.
Care should be given in the use of tools, so that the rubber jars or covers are not damaged. If the cells have been sealed, the sealing compound may be readily removed by means of a hot putty knife.
If the battery is to be cleaned and immediately reassembled, then one cell should be handled at a time, otherwise if the battery is to be left out of commission then the treatment need not be limited to a single cell. The element should be lifted from the cell carefully and placed horizontally on a clean bench, the plates resting on their edges. Spreading the plates gently, the hard rubber and wood separators should be removed and the groups separated. If the wood separators are not in very good condition, they should be discarded and new ones used in reassembling. But if they are in good condition, then they must be kept wet either by being frequently sprinkled with water or immersed in a vessel of pure water or electrolyte after being washed. The positive group should be rinsed very carefully so that loose sediment may be washed off but no damage done to the plate by a strong stream.
The negative plates should also be rinsed carefully and if the active material has expanded appreciably pressed back into place. This operation is accomplished by inserting clean pieces of wood between the plates of the negative group. The thickness of these strips should be approximately equal to the thickness of positive plate with wood and rubber separators so that the joints of lugs and straps may not be strained. The group may then be placed in the press and the spongy lead forced back into position.
The spongy lead, when exposed to the air will quickly absorb oxygen and be oxidized with considerable heating. The oxidation may be removed by long charging, but it is not well to allow the plates to heat excessively, so they should be sprinkled with pure water in order to prevent it and reassembled, placed in the jar and the acid added as soon as possible. The positive plates will not heat in the air and need no such attention.
Having thoroughly washed the jars, the element, assembled as in the case of a new battery, is placed carefully in the jar and the solution added without delay. Particular care should be taken to see that the assembly is correct in all details as explained on (page 51). If the old separators have been used, then the jars should be filled with electrolyte of the same specific gravity as that previously in the cell. If, however, new wood separators have been used, then the acid should be 40 points (.040) higher than when the cell was dismantled, in order to compensate for the water in the new separators. After replacing the separator hold-downs and hard rubber covers, the cells may be placed in the trays and after going over the assembly with a low reading voltmeter to determine the correct polarities, burned together. The trays and connections should be thoroughly cleaned before the cells are returned to position. A weak alkaline solution, such as bicarbonate of soda (baking soda), in water, may be used for this purpose after which the trays, when dry, should be given a treatment of acid proof paint. Inspection should be made to see that all connections are correct and secure.
The battery should be given a charge at the finishing rate (pages 27-36), and continued until the voltage and specific gravity of each cell has ceased to rise for a period of ten (10) hours.
It is recommended that a test discharge be made before placing in service so that the condition of each cell may be found correct. The capacity will be slightly less after cleaning than before, but will increase as the battery is worked.
DIFFICULTIES AND THEIR EVASION
Of the different parts of the electric vehicle, the storage battery is the most important and while responsible for some deficiencies is not open to criticism for everything that goes wrong with the vehicle. A general tendency has been to find that there is something wrong and then assume without question that it is the battery. Besides being unjust, such an assumption is not always founded on fact.
The battery is rated in ampere hours and not in
miles so that if the roads be heavy due to mud or
snow, or if the brakes bind, the ampere draw will
be increased and the mileage necessarily reduced.
Brakes, motor bearings and connections should be
frequently inspected so that the energy consumed
in running may be as small as possible. Inefficient
tires are very often a source of trouble. Such tires
may consume more current in locomotion than all
the elements of vehicle and load put together.
However, should the vehicle with the exception of the battery be found in good order, then it is reasonable to look there for the trouble. The most common difficulties encountered in the operation of lead storage batteries in vehicle service are the following:
- Loss of Capacity. Loss of capacity of the battery may be occasioned by avoidable or unavoidable causes. The unavoidable causes are accident and the natural wear and tear incident to its operation in rigorous service, presuming the correct care. The avoidable causes are lack of care either in handling the battery in the garage or in operating the vehicle on the highways. This includes allowing to stand in a discharged condition, failure to repair as soon as possible after the development of a leaky jar or internal short circuit, failure to remove sediment before reaching the bottom of the plates and allowing impurities such as iron, chlorine, copper, and organic matter to find their way into the electrolyte. The specific reasons for loss of capacity and their remedies are given under 2, 3, 4, etc., as they all affect the capacity or output of the battery.
- Sulphation. Sulphation, or the presence of lead sulphate in the active material of the plate in hardened form, not reduced by usual charging is produced by allowing the battery to stand in a discharged condition or by continued undercharge. It stands to reason that if the battery is given the small amount of necessary care as required, then sulphation can only be due to accidental cause, which is either avoidable or unavoidable. Assuming that with the slight education necessary that only the unavoidable will remain, there should be very little possibility of damage from this cause. The remedy should be immediate and thorough as the effects are additive. A thorough overcharge at a low rate followed by several cycles of charge and discharge will usually be sufficient to bring the battery back into good condition.
- Reversal of the Plates. This is a difficulty which arises only in rare instances but might occur when the cell loses capacity and during the discharge its capacity is exhausted before that of the other cells, resulting in current being forced through it, reversing its plates. Under usual conditions this is not a very probable difficulty providing that a regular inspection of voltage and gravity are made, but, should it be found, then the treatment described for Sulphation (No. 2), will usually bring the cell back into condition.
- Shedding of Active Material. It is obvious that the plates of the storage battery are made to give the maximum life with the maximum capacity during that life, but it is only reasonable to allow that they wear out. In this respect they are almost human and during the life of the plates the capacity gradually decreases until finally it is more economical to scrap them and install new. This is an unavoidable cause and can be tempered only by giving the little attention necessary at the correct time. The main cause of shedding or loss of the particles of active material is excessive gassing. The loss of the minute quantities from the plate under the violent gassing shortens the life of the plate. This is probably the most important difficulty and the remedy consists only in prevention which is simplicity itself. Permit only moderate gassing at all times.
- Corrosion of Plates. As the battery in whole or part is furnished by the manufacturer it is chemically pure so far as harmful impurities are concerned and if distilled water and chemically pure sulphuric acid alone be used during the useful life there need be no cause for trouble. However, should impurities such as copper, iron, mercury, chlorine, nitric acid, platinum, organic matter, etc., be introduced the passage of current will cause them to react upon or corrode the active material of the plates. Necessarily this will reduce the capacity of the cells as it will reduce the amount of active material effective in useful chemical reaction. The remedy consists in removing the corrosive agent. This is described under "Electrolyte," page 72.
- Temperature. At high temperatures chemical action takes place more vigorously and physical effects are more pronounced. Thus the action of hot acid upon the plates and separators is unnecessarily severe for the service rendered, resulting in reduced life. The physical effect of the heat upon the rubber jars is to warp them. It is a simple matter under all usual conditions to keep the cell temperature well below 110° F., but should it reach this limit on charge then the current should be interrupted until normal temperature has been attained.
Extremely low temperatures will cause a temporary decrease in capacity. Bringing the battery to its normal operating condition, however, will make the total capacity available. Only in the most unusual instances are difficulties of this nature experienced. Acid of 1. 130 specific gravity will freeze at 0° F., but 1.275 acid will not freeze at 40° below zero.
TAKING OUT OF COMMISSION.
Under certain conditions of service the battery may be allowed to stand for days or perhaps weeks at a time without being discharged, in which case it is necessary only to maintain the proper level of 2" above the plates for the electrolyte by the addition of pure water and to keep in a charged condition. Ordinarily it is not necessary to charge unless over 50% of the capacity has been discharged, but if the battery is to stand idle for weeks it should be fully charged, and in the case of the battery which is to remain idle for several months, it should at least be given an overcharge before and immediately after the period of idleness. The best practice is to give an overcharge once in two weeks and not less in any case than once a month. Where the battery is to stand without use for over four months or facilities are not available for giving the periodic overcharge required, then it is best to take the battery apart for dry storage. Furthermore, if the battery has been used considerably and is about ready for the removal of sediment, then both purposes can be served at the same time by taking apart and cleaning, leaving the battery ready for assembly when needed. The length of time during which a battery may stand in dry storage is very long, as practically no changes take place if the plates have been treated properly.
The battery should be given an overcharge and dismantled as explained under "Sediment," page 82. The positive plates should be rinsed to remove any loose material and allowed to dry when they are ready for storage. In most cases it will be found more practicable to discard the wooden separators. The perforated hard rubber separators, however, may be washed thoroughly and if not damaged, saved for future use. The acid may be carefully poured into a clean carboy and saved. The jars, hold-downs, connectors, etc., unless dam aged should also be very thoroughly cleaned and stored.
After separating the groups from the element, the negative plates may be dipped in pure water and pressed if necessary.
As explained under "Sediment," the negatives will heat to a certain extent while drying and this should be kept a minimum by sufficient sprinkling of pure water. The evaporation of the water will absorb the heat from the plates and allow them to dry comparatively quickly without danger, after which they may be put in storage for an indefinite period.
The parts should be placed in a dry and clean place and protected from dirt, dampness, etc.
The directions for putting the battery into service are identical with those given for assembling and placing in commission of new batteries. In this case, however, the plate lugs remain burned to the straps and unless damaged in handling need no burning as do the plates received separately when new.
BATTERY ACCESSORY SUGGESTIONS
- Hydrometer syringe.
- Double scale portable voltmeter for locating low cells, discharges, etc.
- Earthenware pitcher, two~quart.
- Earthenware crock, 5-10 gallons, for mixing acid.
- Distilled water for flushing.
- Carboy of 1.300 electrolyte.
- Moderately heavy mineral grease for greasing brass terminals.
- Wire jumpers with suitable terminals for connecting trays when charging outside of the vehicle.
- Extra jars and covers.
- Bench or platform truck to hold battery when outside of vehicle.
- Rubber gloves.
- Thermometer.
- Bicarbonate of soda.
LEAD BURNING— MANIPULATION OF HYDROGEN GENERATORS
In the preceding pages frequent mention is made of the method- of connecting the plates into groups and the groups of one cell to those of the next by means of 'dead burning’' the connection. Lead burning, as explained on page 24, consists in applying a flame of sufficient heat to the cleaned lead parts to make them melt and flow together. In this operation solder is not used but pure lead in stick or bar form, for convenience in handling, is used to supply the filling. This requires very little elucidation as it can be readily seen that the lead joint is very easily made since this metal has a very low melting point and it is not oxidized freely at ordinary temperatures.
The flame which is used to melt the metal at the point of application is known as a hydrogen flame and is concentrated and non-oxidizing and is secured in a relatively simple manner, namely by the action of sulphuric acid upon zinc. The acid attacks the zinc and produces hydrogen gas which is conducted through a bottle of water "O” (Fig. 17) to wash out and remove acid spray or zinc dust, as well as to prevent the flame being drawn back into the generator causing an explosion. The gas, conducted to the Burner’s Tee is mixed with air at a slight pressure, forcing it out of the burning tip with a small hot flame.
The complete outfit necessary for lead burning consists of the following parts:
- One hydrogen gas generator.
- One bottle or trap (for cleaning the gas and preventing the flame from drawing back into the generator).
- One air pump.
- One air tank.
- One lead burner's mixing tee.
- One length of 150' of 5/16" soft rubber tubing (cut into lengths as per requirements).
- One blowpipe.
- Set of tips for burning.
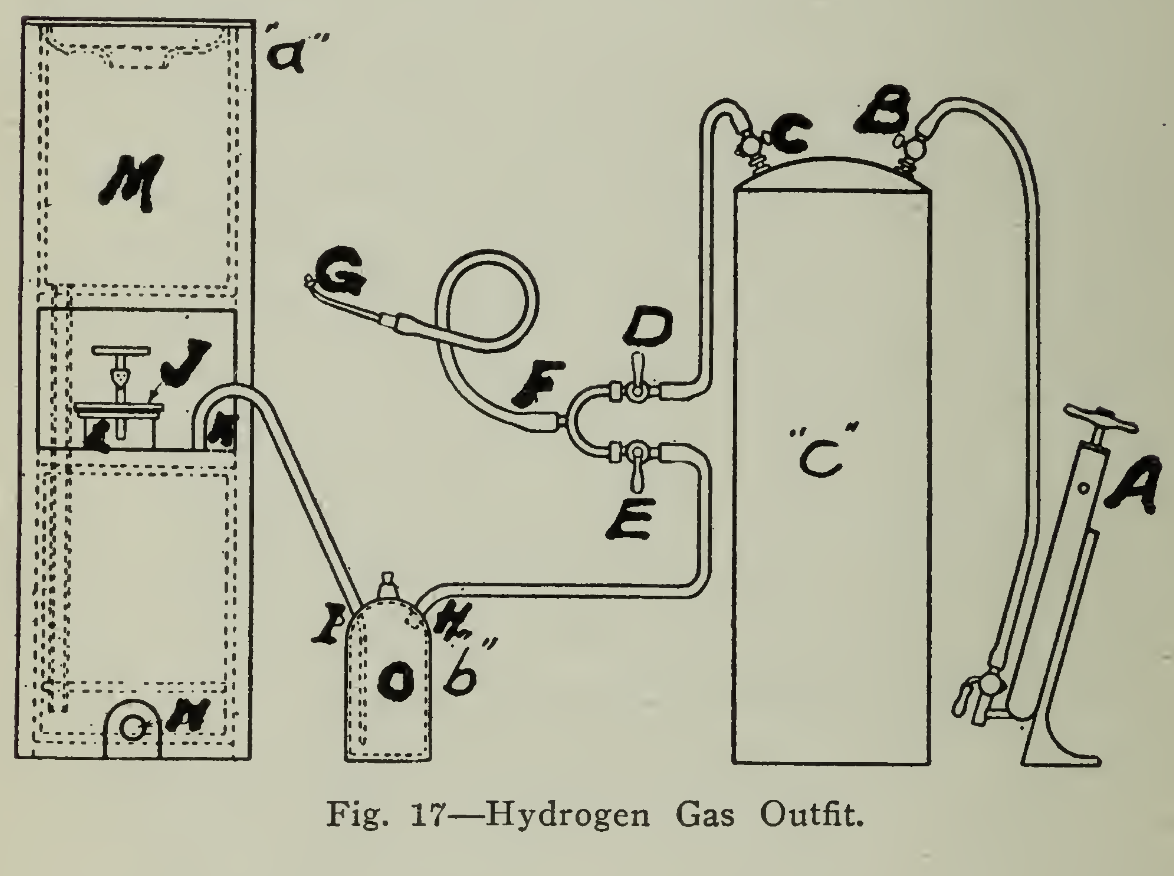
The size of the generator will depend upon the number of flames to be furnished from it. Size No. I is generally used when but one flame is to be operated, while size No. 2 or larger is used depending upon the number of flames to be furnished.
Operation. When the generator is connected for use, the parts will be arranged as shown in the diagrammatic sketch shown on page 96, in which "a" shows the hydrogen generator, "b" the washing bottle or trap and "c" the air reservoir. The bottle should be tilled about two-thirds full with water and connection made to the generator by the tubing "K-I" allowing the tubing to reach to the bottom of the bottle as shown in the drawing "b” Should this bottle become heated, it should either be placed in a pail of cold water, reaching to its neck, and the water replaced from time to time as it becomes hot or immersed in cold running water. The required amount of granular zinc ("spelter”), broken into pieces sufficiently small to allow their insertion at the opening "L” should be put in the generator and the cover "J” clamped down securely. Into the upper portion of the generator "M” the proper amount of water is then added before pouring the required amount of acid, "Oil of Vitriol” (Sulphuric Acid, but not chemically pure). Remember that the acid is to be poured into the water and very carefully to prevent splashing out. Should any acid find its way onto the skin, oil should be applied rather than water. The main point is to get it off quickly.
The length of hose from the mixing valves "D” and "E”‘ to "G” should be no longer than necessary for convenient handling so that the gas and air valves "D” and "E” can be within ready reach and easy control of the operator. The air pump "A" is used to create the air pressure in the reservoir so that when the pumping is discontinued the cock "B" is closed until further pumping is necessary. The cock "C" is opened and with that of "D" closed the gas is allowed to escape from the burning tip by opening the cock "E" and is lighted with a match or candle. When the gas is ignited "D" is opened and the flame regulated by closing "E" until the adjustment gives a flame which will melt the lead leaving a clean bright surface. Trial of scrap lead will show a correct adjustment and the flame is then ready for use.
The size of the burning tip used will depend upon the character of work to be done ; usually all the lead burning required in vehicle work can be accomplished with the tips with small holes. The adjustment of gas and air will also vary the size and flame to suit almost all conditions.
The apparatus should be set up in such a manner that there is no possibility of water discharging over into the tube between "H" and "E" as it is evident that this would discontinue the flame and add dirty water either onto the straps or bars or into the cells. Should water be formed by condensation in this length of tubing, however, it may be removed by kinking the hose between "K" and "I," detaching the tubing at and allowing the pressure in the air tank to force the water out by opening the cocks "E" and "C."
The amounts of zinc given in the table are usually sufficient for three renewals of water and acid so that when the charge is exhausted or the operation is discontinued for a night or any period. The solution should be drawn off and the generator flushed out with water poured into the upper chamber. The new acid should not be added until it is to be used. Before discharging the solution from the generator, the tubing at "H" and "K" should be removed before taking out the rubber plug at "N." As this acid solution is corrosive, it should not be allowed to come in contact with anything near to it or be thrown where it may have opportunity to damage the boarding, asphalt, cement, etc. When discharged into the plumbing, the latter should be well flushed immediately in order to prevent any action upon the piping or fittings.
Its action upon most substances can be counteracted by the quick application of alkaline substances such as ammonia, washing soda and the commercial cleaning compounds ("Gold Dust," "Dutch Cleanser," "Pearline,” etc.).
MATERIAL REQUIRED IN STARTING UP A GENERATOR
Number | Size of Generator | Zinc | Water | Vitriol |
---|---|---|---|---|
No. 1 | 15" X 15" | 20 lbs. | 9 gals. | 2 gals. |
No. 2 | 18" X 18" | 25 lbs. | 12 gals. | 3 gals. |
If the work does not demand the quantity of hydrogen generated in this apparatus then tanks of hydrogen and oxygen or compressed air may be purchased and readily connected to. the mixing tee. If there is available a supply of air under pressure, then the tank of compressed air may be dispensed with. It will probably be necessary to use a reducing valve as two (2) pounds pressure per square inch is usually sufficient for the purpose. Figures No. 12 and 13 show the burning box and burning rack used in burning the plates into the straps.
A device for accomplishing the results given by the hydrogen flame is shown in (Fig. 18) and consists of a clamp with insulated wire attached to a carbon electrode mounted on an insulated handle.
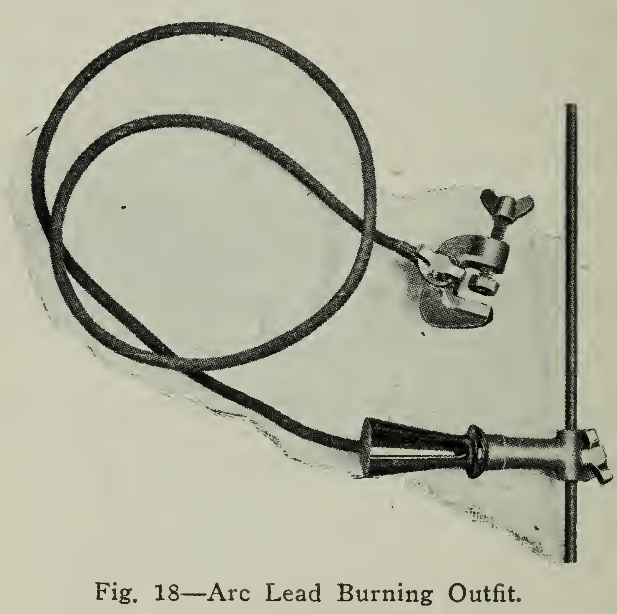
The clamp is attached to the connecting strap of a cell near the one upon which the burning is to be done. In this manner by connecting across 5 cells, a potential of ten volts is available for the arc. The connections should be made so that the carbon is the negative pole. The carbon may then be used as a soldering iron. The materials used in this case are identical with those used in the operation of the hydrogen flame excepting that the heat is produced by the arc instead of the hydrogen generator. In work involving the use of an arc it is always well to wear blue glasses to protect the eyes.
Where neither of these methods are available for mending connections, as for instance, the breaking of a connector upon the road, a soldered joint may be made for temporary use. This, however, is only for the purpose of reaching the garage where the proper treatment can be given.
At all times when the parts of the cells are lead burned or the elements connected, care must be given that strips of lead or pieces of solder do not gain access to the ceil or flow between the plates as this "flow-down" would be likely to make contact between the plates, contaminate the electrolyte or do other damage.