Last Update: February 20, 2019
The mechanism driving an electric car is the same as powers a household fan, or an electric lawnmower, or a power drill. Electricity moving through a wire forms a magnetic field around the wire. With the right design, this fact of nature can be used to drive an electric motor, causing any kind of machine to operate.
In an electric car the electricity is stored in a large battery pack. There are many battery powered devices in use all around us, from flashlights to cell phones to computers to electric shavers and on and on.
Between the battery pack and the electric motor is circuitry, the Controller, that controls how much voltage/current is delivered to the motor. The more voltage/current that's delivered the faster the vehicle will go (roughly speaking). Typically a human is manipulating a throttle, such as the accelerator pedal, to instruct the controller how fast to make the car go. In an autonomous drone vehicle, the throttle is instead controlled by software.
Electric motors
The basic principle of an electric motor is the interaction of two electromagnetic fields. At least one of the fields will be generated by electricity moving through wire coils. The other magnetic field will be generated either by magnets, or by electricity moving through another set of wire coils. The design always includes a rotor (the rotating part) and a stator (the stationary part), with the electromagnetic field interaction causing the rotor to turn.
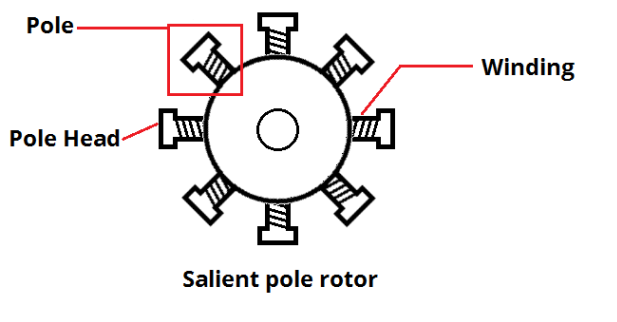
In a Rotor of this sort, electricity must somehow get to the coils in order to form the electromagnetic field. Several ingenious methods are used in the various types of motors.
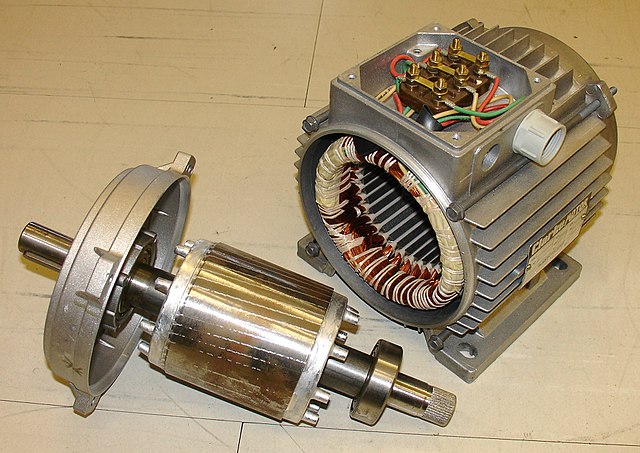
We don't have to get into the details of every kind of electric motor. There are many more parts to electric motors such as bearings, and comutators. For our purpose here, we only need a broad-brush outline of how electric motors work.
Types:
- AC motors are given an AC current, DC motors are given a DC current.
- Brushed motors use soft lead "brushes" to communicate electricity to the Rotor
- Other mechanisms are used to communicate electricity to the Rotor, since Brushes are not terribly reliable and wear out over time
The spinning part (Rotor) and the stationary outer part (Stator) both contain something which forms magnetic fields, either magnets or electromagnet coils. The magnetic fields interact, causing the Rotor to rotate. The rotation is brought out of the motor on a shaft, and that shaft is connected to other equipment. For example in a power drill, the shaft is directly connected with the drill bit. In an electric car, a gear box connects the electric motor shaft to the drive shaft(s) and wheels. In an electric motorcycle, either a chain drive or belt drive mechanism is used to connect electric motor to the rear wheel.
Battery pack
Battery packs are what lets an electric vehicle drive beyond the reach of an extension cord.
For example corded and cordless power drills are essentially identical. The corded variety has a cord that's plugged into a power outlet, while the cordless variety has a battery pack. The cordless power tool can be used anywhere, and there's no hassle of dealing with the power cord.
Electricity by itself is not storable. Battery packs store electricity using an electrochemical reaction. The different types of battery (lead-acid, nickel-metal-hydride, lithium-ion, etc) are named for the elements used in the chemical soup in the particular battery.
Recharging such a battery is accomplished by connecting the battery to a power source. A charger is used to control the charging process. The as power flows into the batteries, electrochemical changes occur storing energy in the form of chemical reactions within the battery.
The electric motor is powered by discharging the battery through the motor. This causes the other electrochemical changes required to release electrons from the chemicals in the battery pack. Those electrons flow through the electric car wiring, through the electric motor, and land back in the battery but in a way that produces the "discharged" electrochemical state.
The big advance in batteries that enabled modern electric vehicles is reliable automotive grade lithium-ion batteries. Previous battery chemistries were used in building electric vehicles, but entailed a higher weight-to-energy-stored ratio than would result in a practical electric vehicle for the masses.
The energy stored in a battery is measured in kiloWatt-hours. One kiloWatt-hour is equal to 1000 Watts of electricity flowing for one hour. If this helps to visualize how much this is, 1,000 Watts is equal to ten 100 Watt light bulbs, or typical hair dryers run at 750 Watts.
In a vehicle, electricity consumption is measured in miles traveled per kiloWatt-hour. Hence, with a 24 kiloWatt-hour battery pack electric cars typically traveled 70-80 miles, and with an 85 kiloWatt-hour battery pack they had 270 miles range or so. The actual range based on battery pack size is dependent on many factors, such as overall vehicle weight.
The advancement named earlier is that lithium-ion batteries enabled two breakthroughs:
- More kiloWatt-hours stored per kilogram of battery weight.
- More kiloWatt-hours stored per liter of battery volume.
The size and weight of the battery pack, relative to the energy it stores, is what determines how practical an electric vehicle can be built.
Future electric vehicle batteries are expected to store much more energy in the same (or smaller) size and weight. That should make batteries cheaper, and make electric cars lighter weight and more efficient.
Battery management systems
Lithium-ion batteries are finnicky enough to require specialized circuitry to monitor the batteries during charge and discharge to ensure the battery is operated within safe parameters. The battery can be damaged if the cells are overcharged or undercharged or if they are discharged at too-high a rate. The battery management system watches all that to keep the battery pack within safe parameters at all times. That electric vehicles are being sold to anyone, who don't care a bit about managing battery pack health, is because of automotive engineers doing a good job on battery management system design.
Any battery pack is built from battery cells. For example a 1.5 volt AA battery is a single battery cell, while the 12 volt lead-acid battery in a car is built from eight cells each about 1.5 volts.
Battery management systems connect with each cell in the battery pack, monitoring the voltage in each cell. For lithium-ion batteries there is a low-voltage threshold where the cell will be damaged if it goes below that level, and there is a high-voltage threshold where other bad things can happen if the cell becomes overcharged. The battery management system then must communicate with the charging system, telling the charger to slow down as the battery reaches full charge, and with the Controller to slow the vehicle down if the voltages drop too low.
Controller
As we said earlier, what connects the battery and the electric motor is a Controller.
As an analogy, think of the Controller as a dimmer switch where you turn a knob to change the brightness in a room. An in an electric vehicle, the driver adjusts the throttle to change the speed the vehicle travels.
The type of controller must match the type of electric motor. For an AC motor, the controller produces the AC waveform required to drive the motor, adjusting both the frequency of the AC waveform and the amperage. For a DC motor, the controller is primarily adjusting the amperage.
Speed is determined by Wattage (Volts x Amps) going into the motor. The actual drivable range is determined by how well the driver can hold back lead-foot tendencies. Traveling at higher speed means getting fewer miles per kiloWatt-hour, and therefore getting less distance traveled for the total energy stored in the battery pack.
Of course the same is true for gasoline/diesel driven vehicles. Higher speed consumes more fuel per mile, meaning the vehicle can go less distance for the total energy/fuel in the fuel tank.
Drive train
The spinning electric motor causes the wheels to spin causing the vehicle to move.
This isn't terribly different from vehicles driven by other fuels. The primary difference is that electric vehicle drive trains do not need a "Neutral" mode that disconnects the motor from the wheels. Instead there is a dedicated mechanical connection between electric motor and the wheels.
In a gasoline/diesel vehicle, the engine cannot stop. Therefore to stop at a stoplight, or other scenarios, the engine must be disconnected from the wheels, otherwise the engine would stall. That disconnection happens in the transmission, and in a manual transmission car the driver manages that disconnect using the clutch pedal.
In an electric car, the motor simply stops spinning. Because electric motors can immediately spin up to any power level (that 100% torque off the line) instantaneously, it is not necessary to keep an electric motor spinning. The car pulls to a stoplight, and the motor stops spinning, and that's it.
Likewise, in an electric motor forward or reverse is simply a matter of changing around the electrical connections. In a gasoline/diesel vehicle, forward or reverse is accomplished in the transmission. Therefore electric vehicles do not need mechanical forward/reverse gearing.